در جهان امروزی، پس از پیشرفتهای صنعتی و تکنولوژی بسیاری که دنیای صنعتی شاهد آن بود، شیوه های نوین بیشماری جهت تولید، شکلدهی و فرآوری مواد روی کار آمدند.
یکی از فرآیندهای نوین و بسیار کارآمد جهت شکل دهی و برش مواد، عمل اکستروژن است؛ اما ابزاری که فرآیند اکستروژن به وسیله آن انجام میگیرد، دستگاهی به نام اکسترودر است.
اکسترودرها در صنایع مختلفی کاربرد دارند و امکان تعمیر یا تولید انواع قطعات و محصولات را به کاربران خود میدهند.
در ادامه این مطالب، به بررسی دقیق و جزئی عمل اکستروژن و دستگاه انجام دهنده آن یعنی اکسترودر میپردازیم. تا آخر این مقاله با ما همراه باشید تا به پاسخ سوال خود (اکسترودر چیست ؟ ) برسید.
اکسترودر چیست؟
اکسترودر دستگاهی کاربردی و پیشرفته است که در صنایع متنوع جهت شکل دهی مواد اولیه و تبدیل آنها به قطعات یا محصولات جدید کاربرد دارد.
فرآیند قالب گیری و برش به وسیله اعمال فشار و حرارت به مواد است، به طوری که مواد با فشار از یک قالب خاص و پیش طراحی شده عبور داده میشود. این عمل در صنایعی مثل پلاستیک، مواد غذایی، داروسازی و ... کاربرد گستردهای دارد.

اجزای اصلی دستگاه اکسترودر
استراکچر دستگاه
فریم کلی یا بدنه دستگاه استراکچر نام دارد که تمامی قطعات دیگر بر روی آن نصب میشود.
قیف تغذیه
قسمت قیفی شکل است که محل تغذیه داخل دستگاه است و مواد اولیه از طریق آن به دستگاه تغذیه میشود.
سیلندر
محفظهای که در آن فشار و حرارت به مواد وارد میشود.
ماردون
قطعهای که به شکل مارپیچ است و همزمان با اینکه مواد را به جلو هدایت میکند، آنهارا ذوب و یکنواخت نیز میکند.
المنتهای حرارتی
المنتهایی که حرارت لازم جهت ذوب کردن مواد را به آنها میدهد.
سنسورهای دما وفشار
سنسورهایی جهت نظارت و کنترل فرآیندهای عملیات در اکسترودر کار گذاشته میشود.
پمپ دندهای
در برخی مدلهای اکسترودر، از پمپها جهت تنظیم فشار استفاده میشود.
قالب
بخشی است که مواد ذوب و آماده شده نهایی به آن منتقل میشود.
سیستم خنک کننده
همان فنها یا کانالهای آب هستند که جهت کاهش دما و حفظ شکل مواد خروجی در دستگاه الکترود جای گذاری میشوند.
موتور گیربکسها
تامین نیرو جهت حرکت دستگاه، به وسیله موتور انجام میگیرد و به وسیله گیربکسها به سایر بخشها منتقل میشود.
تابلو برق یا واحد کنترل
بخش کنترل گر دستگاه است که تنظیم میزان فشار و یا دما و روشن خاموش کردن دستگاه به وسیله آن انجام میگیرد.
سیستم برش
مواد را پس از شکلگیری و آمادهسازی ( خنک کردن )، به حالت از پیش تعریف شده برش میدهد.
انواع اکسترودرها
اکسترودرهای پرکاربرد، انواع مختلفی دارند که هریک از آنها بر اساس نوع کاربرد و نوع دستگاه در صنایع مختلفی مورد استفاده قرار میگیرند. برخی از انواع رایج و پرکاربرد اکسترودرها عبارت اند از :
اکسترودر تک ماردون ( Single Screw Extruder )
اکسترودر تک ماردون یا تک پیچ، از یک پیچ مارپیچی تشکیل میشود، که این پیچ درون یک محفظه (بریل ) قرار دارد. مواد اولیه از سوی قیف تغذیه وارد این محفظه میشود که در اثر حرارت، فشار و نیروی مکانیکی از چرخیدن پیچ، مواد ذوب شده به سمت خروجی حرکت میکند. بر اساس نوع طراحی دستگاه، مواد میتوانند پس از فشردهسازی و همگن سازی منتقل داده شده اند.

کاربردهای دستگاه اکسترودر تک ماردون
+ تولید فیلمهای پلاستیکی
+ تولید محصولات پلیمری
+ تولید محصولات پلیمری
+ تولید محصولات غذایی مثل پفک یا پاستا
+ و ... اشاره کرد.
این اکسترودر ( تک ماردون یا تک پیچ ) با داشتن ساختاری ساده و نگهداری آسان و کم هزینه، پرکاربردترین و رایج ترین نوع اکسترودرها محسوب میشود.
اکسترودر دو ماردون ( Two Screw Extruder )
ساختار این نوع اکسترودر، همانند اکسترودرها تک ماردون، از پیچ مارپیچی تشکیل شده با این تفاوت که تعداد مارپیچ آن، دو عدد است که به طور موازی کنار یکدیگر قرار گرفتند. این نوع اکسترودر بیشتر برای مواد با ویسکوزیته بالا که فرآیندهای پیچیدهای دارند، مناسب است و اختلاط و پراکندگی یکنواخت برای محصول انجام میدهد.
ویژگیهای اکسترودر دو پیچ ( دو ماردون )
+ قابلیت یکنواخت مواد
+ قابلیت کنترل بیشتر بر روی مواد خروجی از دستگاه
+ امکان تنظیم فشار و دما به حالت دلخواه
دستگاه اکسترودر مخلوطی
دستگاه اکسترودر از نوع مخلوطی، همانطور که از نامش پیداست از استوانههای مخروطی شکل که قطر آنها قابل تغییر است، تشکیل شده است. متغیر بودن قطر این استوانهها، این امکان را به کاربران آن میدهد که در صورت تمایل و نیاز، در حین عملیات، مقادار فشار یا حرارت دستگاه را زیادتر کنند.
اکسترودر مخروطی، جهت کاربرد در صنایع سنگین و ساخت لولههای ضخیم است که نیاز به تراکم بیشتری دارند.
اکسترودر دیسکی
در ساخت اکسترودر دیسکی به جای پیجهای مارپیچ، از دیسکهای متحرک چرخان استفاده میشود که بتواند مواد را به سمت خروجی هدایت کند. این نوع اکسترودرها ( دیسکی ) اغلب در صنایع غذایی یا دارویی کاربرد دارند که بتوانند همگنسازی بیشتری ایجاد کنند.
به حالت کلی، همه نوع دستگاههای اکستروژن، با توجه به عملکرد خود جهت کاربرد خاصی طراحی شده اند.
اکسترودرهای دو ماردون برای ترکیب مواد با ویسکوزیته بالا، اکسترودرهای تک ماردون، برای تولید محصولات استاندارد و الکترودهای خاص مثل اکسترودرهای دیسکی یا مخروطی برای کاربردهای خاص طراحی شدهاند.
ویژگیهای کاربری اکسترودرها
قابلیت فرآوری مواد متنوع
اکسترودرها معمولا انعطافپذیر هستند و در اکثر صنایع کاربرد دارند، مثل : مواد غذایی، صنایع دارویی، پلیمیری و ...
قابلیت کنترل دما و فشار
بسیاری از دستگاههای اکسترودر، به صورت پیشرفته هستند و میتوانند کنترل دما یا فشار را انجام دهند و باعث بهبود کیفیت محصول شوند.
قابلیت تنظیم سرعت و میزان تولید
سیستم تنظیمکننده حرکت دستگاه و منتقلکننده (موتور گیربکس ) به گونهای طراحی شدهاست که کاربران بتوانند سرعت دستگاه را تنظیم کنند.
سیستم خنککننده و گرمایشی پیشرفته
وجود المنتها جهت حرارت دهی و سیستم کولینگ (خنک کننده ) جهت تنظیم دمای مواد خروجی تنظیم شده اند و باعث بهبود کیفیت آنها میشوند.
ضایعات تولیدی بسیار کم
اکسترودرها معمولا ضایعات کمتری نسبت به باقی دستگاهها تولید میکنند و از هدر رفت مواد جلوگیری میکنند، لازم به ذکر است که از ضایعات لاستیک یا پلاستیک در این دستگاه استفاده مجدد میگردد.
طول عمر بالا و نگهداری آسان
اکسترودرهای جدید و پیشرفته به سیستمهای کنترل PLC مجهز هستند و امکان نظارت و تنظیم دقیق فرآیند تولید را به کاربران میدهند.
مصرف انرژی کم
اکسترودرها به گونهای طراحی شده اند که مصرف انرژی در آنها بسیار کم بوده و بازدهی زیادتری دارند.
کاربردهای اکسترودر در صنایع
همانطور که در بخشهای قبل به آن اشاره شد، اکسترودر به عنوان یکی از تجهیزات مهم و کاربردی در فرآوری و شکلدهی مواد است و با داشتن ویژگیهای منحصر بفرد، تبدیل به دستگاهی ایده آل شده و در صنایع مختلفی کاربرد دارد. برخی کاربردهای دستگاه اکسترودر عبارت اند از :
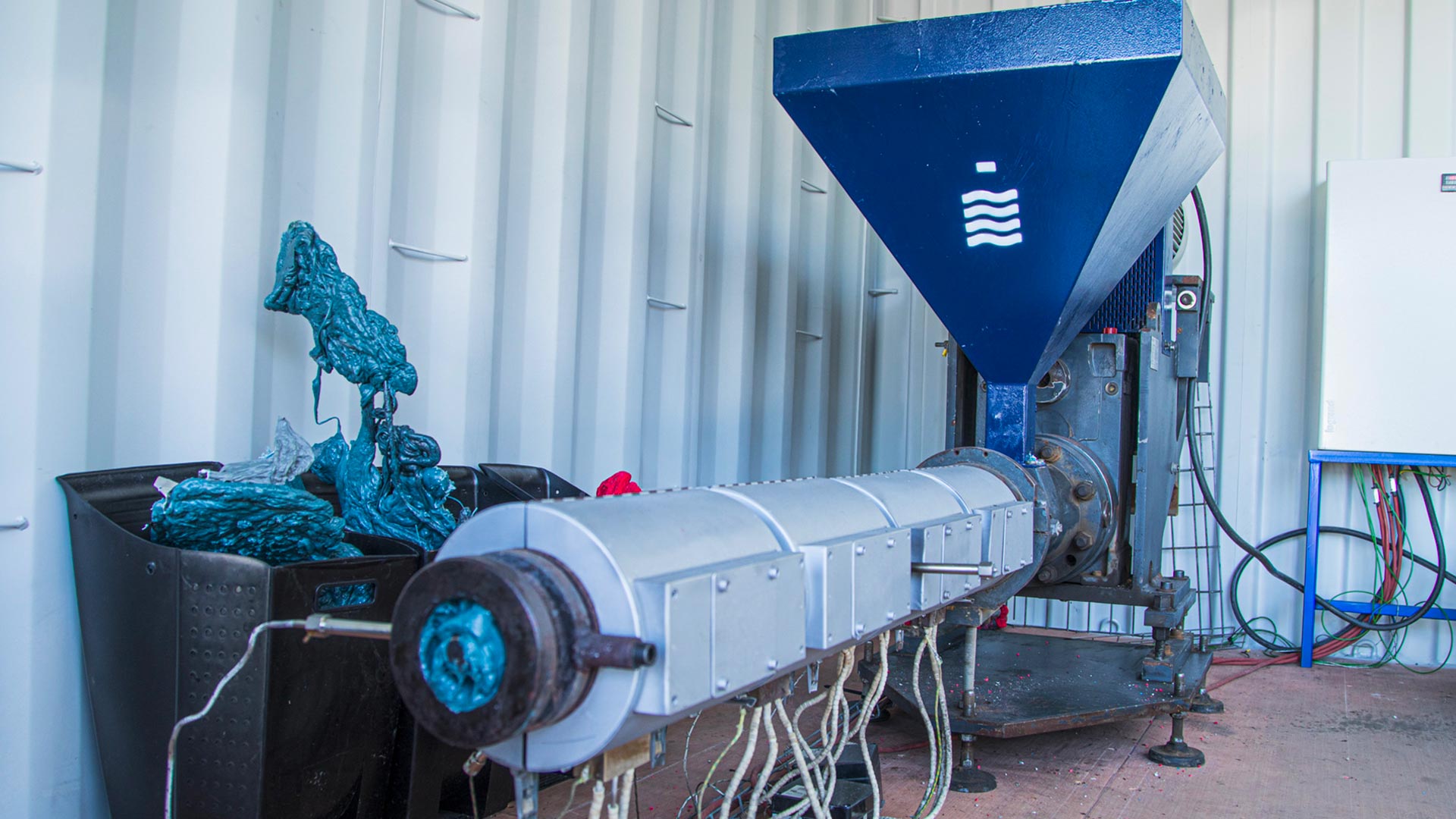
اکسترودر در صنعت پلاستیکی
صنعت پلاستیکی و پلیمری از صنایع مهم و تخصصی است که دستگاه اکسترودر در آن کاربرد ویژه دارد.
از دستگاه اکسترودر، جهت تولید لولههای پلاستیکی، PVC یا پلی اتیلن به کار میرود که در نهایت برای صنایع آبرسانی، گاز رسانی یا فاضلاب و ... کاربرد دارند.
+ اکسترودرها همچنین در تولید پروفیلهای پلیمری و شکل دادن به پروفیلهای PVC و ABS استفاده میشوند که در صنایع ساختمانی، خودروسازی و ... کاربرد دارند.
+ در تولید فیلمهای پلاستیکی مثل پلی اتیلن و پلی پروپلین، دستگاههای تخصصی و پشرفته اکسترودر به کار میروند؛ سپس از این فیلمها در تولید کیسههای پلاستیکی و صنایع بستهبندی بهره برده میشود.
اکسترودر در صنعت مواد غذایی
فرآیند فرمدهی و شکلدهی به مواد اولیه غذایی، توسط اکسترودرها انجام میگیرد. مثلا : برای تولید پفک و اسنکهای حجیمشده، آرد یا نشاسته از اکسترودر عبور داده میشود و سپس منبسط میشود.
+ در تولید پاستا و رشتههای غذایی نیز، ترکیب مواد اولیه مثل آب و آرد از طریق قیف تغذیه وارد اکسترودر میشود و پس از عبور از آن به حالت خاص درآمده و به اشکال مختلف مانند : ماکارانی یا نودل و ... تبدیل میشوند.
اکسترودر صنعت خوراک دام و طیور
از اکسترودرها در تولید خوراک دام استفاده میشود، به این دلیل که خوراکیهای تولید شده توسط اکسترودرها قابلیت جذب بالا و هضم بهتر دارند.
اکسترودر صنایع شیمیایی و پتروشیمی
+ در صنایع شیمیایی، جهت تولید مستربچ و ترکیبات رنگی برای پلاستیکها؛ میتوان از دستگاه اکسترودر بهره برد.
+ تولید مواد تقویت شده مثل کامپوزیتهای پلیمری توسط دستگاه اکسترودر انجام میگیرد.
نگهداری و تعمیرات دستگاه اکسترودر
دستگاه اکسترودر از مقاومت بالایی برخوردار است و این به دلیل کاربرد مواد اولیه با کیفیت در ساختار آن است، اما نگهداری درست و استفاده از آن در شرایط محیطی مناسب میتواند باعث افزایش طول عمر و بهرهوری دستگاه شود. در ادامه مطالب به بررسی برخی نکات نگهداری از دستگاه میپردازیم :
+ با بررسی دورهای و مرتب قطعات دستگاه اکسترودر، میتوانید در صورت وجود ایراد یا مشکلی از آن باخبر شده و فورا آن را حل نمایید.
+ تمیزکاری مرتب دستگاه سبب افزایش طول عمر دستگاه میشود چرا که از تجمع گرد و غبار و آلودگیها درون دستگاه جلوگیری میکند.
+ روغنکاری منظم دستگاه میتواند به بهبود کارکرد آن به صورت روان تاثیر گذارد.
+ دمای مناسب برای استفاده یا تمیزکاری دستگاه فراهم کنید.
+ آموزش پرسنل میتواند تاثیر شایانی در بهبود عملکرد دستگاه بگذارد و ایمنی کاربران دستگاه را افزایش میدهد.